ERP(EnterpriseResourcePlanning)即企业资源计画,是针对物资资源管理(物流)、人力资源管理(人流)、财务资源管理(财流)、信息资源管理(信息流)集成一体化的企业管理软体。它是由早期的物料资源计画MRP(MaterialRequirementPlanning)演变而来,目前绝大部分ERP产品的核心算法与MRP算法相同。主要围绕以下问题展开:库存够不够?什幺时候需要採购?採购的量是多少?
基本介绍
- 中文名:企业资源计画
- 外文名:EnterpriseResourcePlanning
基本逻辑
ERP算法的基本逻辑可以分以下几个方面,如下图所示:ERP算法基本逻辑 1、确定需要什幺产品,生产量是多少。
2、通过BOM分解生产这些产品需要哪些物料。
3、获取已有库存的物料信息。
4、计算还缺的物料信息。
5、计算安排生产製造的开始和结束时间。
这种系统运算逻辑适合于计画比较稳定、需求变化不大的MTS(面向库存生产)的企业进行资源管理。
ERP算法基本逻辑
2、通过BOM分解生产这些产品需要哪些物料。
3、获取已有库存的物料信息。
4、计算还缺的物料信息。
5、计算安排生产製造的开始和结束时间。
这种系统运算逻辑适合于计画比较稳定、需求变化不大的MTS(面向库存生产)的企业进行资源管理。
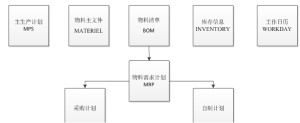
相关计算
1、计算毛需求Demandrough(t)
毛需求量就是指在计画时间内对物料的总需求量,分两种情况。一种情况是独立需求件,该需求通过分解主生产计画得到;还一种是相关需求件,通过计算公式:
Demandrough(t)=∑_(i=1)^n▒〖Di(t)*Qi〗
其中Di(t)是指的物料的第i个父项在第T时段计画下达数量,Qi为单位第i个父项所需子项的数量,通过BOM分解得到。
2、计算净需求G(t)
净需求量G(t)=Demandrough(t)-V(t)
V(t)为有效库存量v(t)=S(t)-A(t)+R(t)-safestock
S(t)为当前库存量,A(t)为已分配库存量,R(t)为预计到货量(在途量),safestock为安全库存量。
3、计算计画产出量P(t)
计画产出量其实就是Demandrough(t),不过需要考虑到经济订货批量或经济生产批量或最小订货量(EOQ)。
4、计算计画投入量R(t)
考虑到废品率p,计画投入量R(t)=P(t)*(1-p)
5、计画期末库存量H(t)
期末库存量就是指某物料在计算周期t的期末的库存量,分两种情况。当毛需求量大于上一期期末库存量减去安全库存量,则当期期末库存量为计画产出量P(t)减去净需求量G(t),反之如果毛需求量小于等于上一期期末库存量减去安全库存,则当期期末库存量为上期期末库存减去毛需求量Demandrough(t)。
毛需求量就是指在计画时间内对物料的总需求量,分两种情况。一种情况是独立需求件,该需求通过分解主生产计画得到;还一种是相关需求件,通过计算公式:
Demandrough(t)=∑_(i=1)^n▒〖Di(t)*Qi〗
其中Di(t)是指的物料的第i个父项在第T时段计画下达数量,Qi为单位第i个父项所需子项的数量,通过BOM分解得到。
2、计算净需求G(t)
净需求量G(t)=Demandrough(t)-V(t)
V(t)为有效库存量v(t)=S(t)-A(t)+R(t)-safestock
S(t)为当前库存量,A(t)为已分配库存量,R(t)为预计到货量(在途量),safestock为安全库存量。
3、计算计画产出量P(t)
计画产出量其实就是Demandrough(t),不过需要考虑到经济订货批量或经济生产批量或最小订货量(EOQ)。
4、计算计画投入量R(t)
考虑到废品率p,计画投入量R(t)=P(t)*(1-p)
5、计画期末库存量H(t)
期末库存量就是指某物料在计算周期t的期末的库存量,分两种情况。当毛需求量大于上一期期末库存量减去安全库存量,则当期期末库存量为计画产出量P(t)减去净需求量G(t),反之如果毛需求量小于等于上一期期末库存量减去安全库存,则当期期末库存量为上期期末库存减去毛需求量Demandrough(t)。
用途与性质
进行资源管理
为了提升管理水平,我国的按单製造(MTOII)型企业在经历了多年的摸索之后,也开始向信息化方向发展。但是,按单製造(MTOII)与批量製造、定型製造等有着显着的区别,传统的基于BOM的ERP系统并不适用于这种生产模式。
1、按单製造(MTOII)的产品具有多样性和唯一性
多样性是指按单製造的产品种类多;唯一性是指这些产品一般不再会重複生产。通常,批量生产的产品,只需建立一个标準的BOM和生产工艺路径(Routing),之后成千上万的产品都可以反覆引用。而按单製造(MTOII)模式下的产品,BOM和Routing很可能在一单生产完成后就再也用不到了。生产产品所需要的物料清单(BOM),如果用ERP的方法来维护,就会造成每生产一个新产品都要新建一个的BOM的情况,鑒于产品只做一次,或者很少的几次,也就是可复用性为零,按单製造(MTOII)企业通常就不会有热情去维护BOM,这也就会造成“ERP不好用”的抱怨。其实,对按单製造企业来说,最需要的是产品结构,而不是物料清单,因为产品结构决定了相似性高的同一製造类产品的用料结构和工艺结构,这可以成为最终物供和生产的“原型”。只有适应这种按单生产模式,才能受到操作者的欢迎。
2、按单製造(MTOII)产品无法进行小批量试产
按单製造(MTOII)产品没有机会像批量化生产那样进行小批量试产。因为其产品单台价值大,也有可能体积大,加工难度高,企业多半是通过设计阶段的仿真模拟来论证产品的性能和质量特性。投产的前提是客户订单而非产品定型需要。最初的製造工艺会随着生产过程中出现的问题,及时修改某个部件的材料需求或Routing。通常我们将按单製造(MTOII)的标準分为三级:产品级、製造级和作业级。如果用传统ERP的方式操作,因为是定型后才允许大规模生产,ERP只有产品级的製造标準,这样一来,每一次修改都会影响产品的整个BOM结构,在其维护的工作量巨大的同时,还会影响后续产品的生产。用传统ERP的解决方案来管理按单製造,是无法使用的。
3、按单生产的产品生产周期较长
按单製造(MTOII)产品根据其性质和难度的不同,产品生产周期从3个月到2年不等,有的甚至需要3~5年。如此长的生产周期,生产管理的变数自然非常大。并且由于其生产工艺複杂,需要在不同的生产车间,不同的机台,不同的操作者之间不断地转移,依据传统EPR的工作原理,会将每一个加工件在不同车间之间的流转先做出入库处理,由此来用新的物料编码区分不同的生产状态,并在BOM上有所反映。这样一来,只要按单生产存在变数,BOM以及其基础数据物料都将发生变化。在长生产周期下这种变化的结果是失去了标準,也就是失去了管理这种变化的依据,造成无效的信息化管理的现象。
综上所述,当前市场上成熟的ERP软体,本身是强大的。但可惜它是以上世纪70、80年代欧美国家,根据大批量定型产品的生产模式设计出来的,主要适用于对批量产品的管理。按单製造企业指望不了传统ERP,而是要採用基于按单製造原理设计的MTOII管理软体和解决方案去实现,也就是说市场呼唤着按单製造ERP的诞生。
1、按单製造(MTOII)的产品具有多样性和唯一性
多样性是指按单製造的产品种类多;唯一性是指这些产品一般不再会重複生产。通常,批量生产的产品,只需建立一个标準的BOM和生产工艺路径(Routing),之后成千上万的产品都可以反覆引用。而按单製造(MTOII)模式下的产品,BOM和Routing很可能在一单生产完成后就再也用不到了。生产产品所需要的物料清单(BOM),如果用ERP的方法来维护,就会造成每生产一个新产品都要新建一个的BOM的情况,鑒于产品只做一次,或者很少的几次,也就是可复用性为零,按单製造(MTOII)企业通常就不会有热情去维护BOM,这也就会造成“ERP不好用”的抱怨。其实,对按单製造企业来说,最需要的是产品结构,而不是物料清单,因为产品结构决定了相似性高的同一製造类产品的用料结构和工艺结构,这可以成为最终物供和生产的“原型”。只有适应这种按单生产模式,才能受到操作者的欢迎。
2、按单製造(MTOII)产品无法进行小批量试产
按单製造(MTOII)产品没有机会像批量化生产那样进行小批量试产。因为其产品单台价值大,也有可能体积大,加工难度高,企业多半是通过设计阶段的仿真模拟来论证产品的性能和质量特性。投产的前提是客户订单而非产品定型需要。最初的製造工艺会随着生产过程中出现的问题,及时修改某个部件的材料需求或Routing。通常我们将按单製造(MTOII)的标準分为三级:产品级、製造级和作业级。如果用传统ERP的方式操作,因为是定型后才允许大规模生产,ERP只有产品级的製造标準,这样一来,每一次修改都会影响产品的整个BOM结构,在其维护的工作量巨大的同时,还会影响后续产品的生产。用传统ERP的解决方案来管理按单製造,是无法使用的。
3、按单生产的产品生产周期较长
按单製造(MTOII)产品根据其性质和难度的不同,产品生产周期从3个月到2年不等,有的甚至需要3~5年。如此长的生产周期,生产管理的变数自然非常大。并且由于其生产工艺複杂,需要在不同的生产车间,不同的机台,不同的操作者之间不断地转移,依据传统EPR的工作原理,会将每一个加工件在不同车间之间的流转先做出入库处理,由此来用新的物料编码区分不同的生产状态,并在BOM上有所反映。这样一来,只要按单生产存在变数,BOM以及其基础数据物料都将发生变化。在长生产周期下这种变化的结果是失去了标準,也就是失去了管理这种变化的依据,造成无效的信息化管理的现象。
综上所述,当前市场上成熟的ERP软体,本身是强大的。但可惜它是以上世纪70、80年代欧美国家,根据大批量定型产品的生产模式设计出来的,主要适用于对批量产品的管理。按单製造企业指望不了传统ERP,而是要採用基于按单製造原理设计的MTOII管理软体和解决方案去实现,也就是说市场呼唤着按单製造ERP的诞生。